How Tech Helps Cut Equipment Downtime for Landscaping Teams
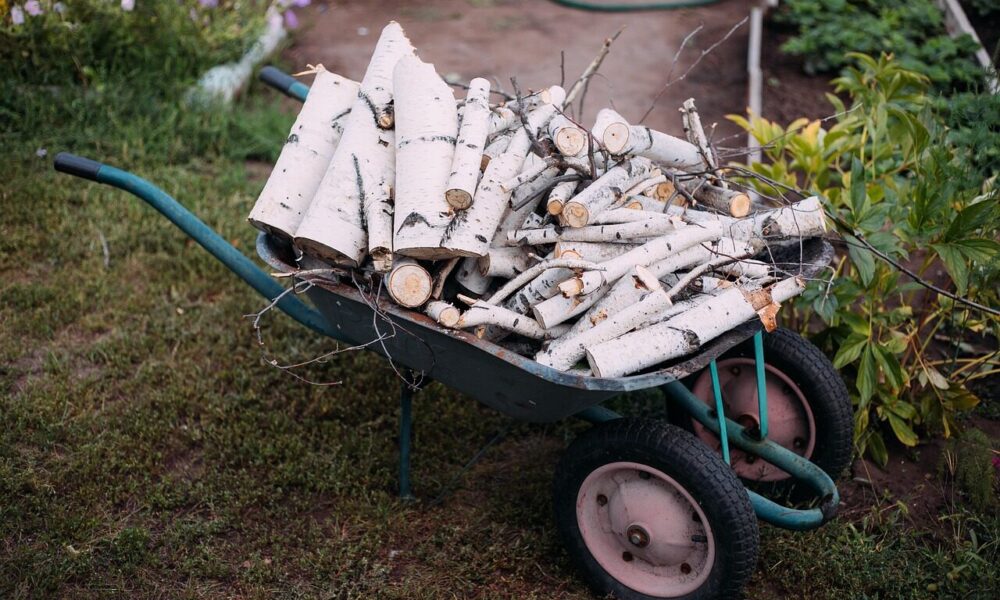
In landscaping, time is money, and nothing eats into both quite like equipment downtime. When mowers, trimmers, or aerators go offline, crews lose precious hours, project timelines are delayed, and client satisfaction can take a hit. As demand grows for faster, more efficient service, minimizing mechanical disruptions has become a top priority for landscape professionals.
Traditionally, many landscaping businesses have handled maintenance reactively, waiting for a problem to occur before addressing it. But this approach no longer makes sense in a competitive environment where reliability, reputation, and speed matter more than ever. The good news is that technology is changing the game.
Smarter Maintenance Tracking With Software Tools
The cornerstone of reduced downtime is better maintenance, and better maintenance starts with organization. Spreadsheets and paper logs, once the standard for tracking service history, are rapidly being replaced by digital platforms that streamline the entire process. Using landscape equipment maintenance software, teams can monitor oil changes, blade sharpening, belt replacements, and more, all from a centralized dashboard. These platforms send automated reminders for upcoming services, log completed tasks, and flag potential issues based on usage patterns or machine hours.
By keeping service schedules consistent and visible to the entire team, these tools reduce the likelihood of missed maintenance. They help extend equipment life, reduce repair costs, and ensure compliance with warranty requirements.
When fleet data is accessible from mobile devices, technicians and crew leads in the field can report issues or update records in real time. This on-the-go visibility promotes accountability, speeds up response times, and gives business owners a full picture of their equipment’s health at any moment.
Real-Time Monitoring for Critical Metrics
Beyond scheduled maintenance, new tech solutions allow for real-time monitoring of equipment performance. Sensors installed on mowers, loaders, or utility vehicles can track metrics like engine temperature, fuel consumption, and operating hours. These insights help predict wear and tear and detect abnormal behavior before it leads to breakdowns.
GPS tracking adds another layer of control. Managers can see where equipment is being used, how long it’s operating, and whether it’s being used efficiently. If a machine idles for extended periods or strays from its intended job site, those issues can be addressed quickly.
Telematics systems, once exclusive to large construction firms or trucking fleets, are now accessible to small and mid-sized landscaping businesses. These systems help eliminate guesswork by turning machine performance into actionable data. When the data reveals inefficiencies or misuse, it enables training opportunities that enhance both safety and productivity.
Streamlining Repairs With Mobile Access
When equipment does fail, fast repairs are critical. Technology helps in this area by improving communication between teams and service providers. With mobile-enabled apps, field crews can submit detailed repair requests, including photos, notes, and diagnostic codes, to mechanics or fleet managers instantly.
Service teams can then prioritize repairs, check part availability, and schedule the fix without delay. Some systems allow for integration with parts suppliers, enabling faster sourcing and reordering of commonly used components.
Digital repair histories make it easier to identify recurring problems. If a mower consistently needs belt replacements or a blower suffers from overheating, the data can help determine whether it’s time for a replacement, a different operator strategy, or a change in product line.
Simplifying Inventory and Parts Management
Unplanned downtime is often made worse by missing or mismanaged parts. One broken spring or a worn-out filter can sideline equipment for days if replacements aren’t on hand. Smart inventory management tools now help landscaping companies track the location and quantity of spare parts in real-time.
With automated alerts, managers are notified when stock runs low, helping ensure critical items are reordered before they run out. These systems reduce waste by identifying obsolete inventory that’s taking up space and tying up capital.
Some maintenance platforms integrate parts tracking directly into service logs, making it easy to see which parts are used most often and what items are important to keep in stock for high-use machines.
Leveraging Predictive Analytics to Stay Ahead
Perhaps the most promising innovation in downtime reduction is predictive analytics. By analyzing years of maintenance records, usage trends, and environmental conditions, advanced software can forecast when equipment is likely to fail. This allows teams to act before a breakdown occurs, saving both time and money.
Predictive models help prioritize which machines need servicing based on risk rather than a fixed schedule. This shift from reactive or even preventive maintenance to predictive maintenance represents a major leap forward in operational efficiency.
Reducing Downtime Through Operator Training and Accountability
Technology supports one of the most overlooked factors in equipment health: the operator. Improper use or lack of familiarity can lead to avoidable damage. Maintenance software can be used to assign operator certifications or track training milestones, ensuring that only qualified individuals handle sensitive machinery.
Digital checklists before and after use allow crews to verify machine conditions, report anomalies, and take responsibility for any issues that arise during their shift. This culture of accountability reduces careless damage and promotes early detection of small issues before they become major failures.
In an industry where every hour counts, the ability to anticipate and prevent issues is no longer a luxury, it’s a competitive advantage. As more landscaping teams embrace these solutions, downtime is becoming less of a burden and more of a manageable factor in building a scalable, resilient business.
Source: How Tech Helps Cut Equipment Downtime for Landscaping Teams