The Future of Asset Tracking in Industrial Environments
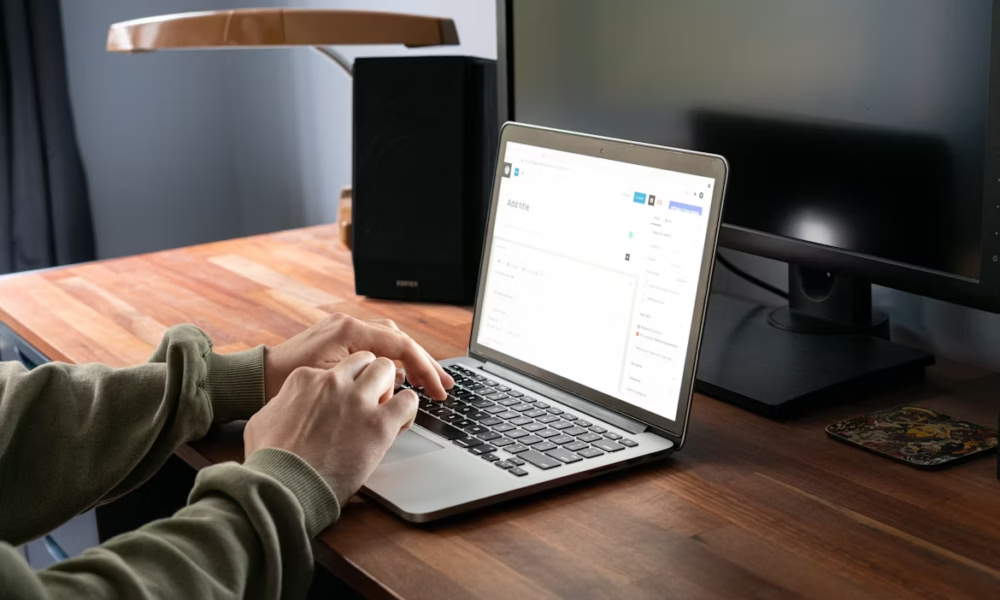
As industrial operations continue to evolve through automation and digital transformation, the importance of precise asset tracking has never been greater. From construction sites and manufacturing plants to large-scale logistics and energy facilities, understanding where your assets are, how they’re being used, and whether they’re performing as expected can directly influence safety, productivity, and profitability.
Businesses can no longer afford the risks and inefficiencies associated with manual inventory counts or delayed asset discovery. The future of asset tracking lies in smart technologies that monitor location and deliver real-time insights to support predictive maintenance, compliance, and seamless coordination across departments.
Smart Tags and Sensors
One of the core technologies revolutionizing asset tracking is the integration of smart tags and IoT-based sensors. These small, durable devices attach to machinery, tools, and mobile assets, transmitting location, temperature, usage patterns, and even vibration levels to centralized software platforms. These sensors form the foundation for advanced industrial location tracking systems, which allow organizations to see exactly where their equipment is at all times. They help prevent losses due to theft or misplacement and ensure critical assets are in the right place at the right time.
With this kind of visibility, maintenance schedules can be optimized, inventory turnover can be managed more effectively, and project timelines are less likely to be derailed by missing gear.
Real-Time Data and Predictive Intelligence
The value of asset tracking has shifted from mere location monitoring to real-time operational intelligence. Modern systems collect a stream of performance metrics that can be analyzed to detect wear and tear, predict malfunctions, or highlight inefficiencies before they become major issues.
In a manufacturing setting, if a conveyor motor starts to show irregular power usage, the system can flag this change, schedule a maintenance alert, and prevent a costly shutdown. Likewise, if field service teams are equipped with smart tablets connected to asset tracking dashboards, they can locate equipment faster, complete work orders more efficiently, and report service logs instantly.
Predictive analytics derived from this data further empowers managers to make strategic decisions based on usage trends, idle time, and lifecycle projections. The days of reactive maintenance are being replaced with proactive asset health strategies.
Integration with Enterprise Systems
Another driving force in the future of industrial asset tracking is seamless integration with existing enterprise resource planning (ERP) and maintenance management systems. When asset data flows into your business’s broader ecosystem, it creates a unified view of operations, from procurement and storage to deployment and retirement.
Integrating tracking tools with ERP platforms simplifies compliance with industry regulations, particularly in sectors such as energy, construction, and aerospace, where audits and documentation are routine. With all asset data time-stamped, geo-tagged, and digitally stored, compliance reporting becomes less about chasing paper and more about unlocking insights.
Scalability and Customization
Industrial environments vary greatly in size, scope, and complexity, which makes scalability a key requirement for any asset tracking solution. Fortunately, modern systems are highly customizable, with modular features that allow businesses to scale as their operations grow.
Whether you’re tracking ten forklifts across a single warehouse or monitoring thousands of components across a nationwide network of job sites, scalable solutions ensure that tracking capabilities evolve with your business. Cloud-based platforms make it easier to manage updates, deploy new tracking modules, and give access to multiple teams, without the need for extensive IT overhauls.
Custom alert configurations, role-based access, and mobile-friendly dashboards ensure that everyone from technicians to top-level executives gets the right data at the right time.
Environmental Resilience and Durability
A key challenge in industrial asset tracking is dealing with harsh environmental conditions. From outdoor construction sites to chemical processing plants, many locations subject equipment to dust, moisture, extreme temperatures, and physical impacts.
To address these issues, hardware innovations have produced ruggedized tags and sensors designed to withstand even the most hostile conditions. These include tamper-proof enclosures, long-lasting batteries, and anti-corrosion coatings. Some devices are built to operate in intrinsically safe zones where flammable gases or materials are present, ensuring full compliance with safety standards.
Durable technology extends the life of your investment and ensures consistent performance, even in places where standard consumer-grade trackers would quickly fail.
AI and Machine Learning
The next frontier in asset tracking lies in artificial intelligence (AI) and machine learning. These technologies will analyze vast data sets gathered by sensors to automate complex decision-making and provide even deeper insights.
Machine learning models can recognize patterns in how specific machines are used under certain conditions and recommend adjustments to prevent breakdowns. AI can assist in route optimization for mobile assets, suggesting efficient schedules for repairs or relocations based on usage intensity, proximity, and downtime requirements.
By investing in modern tracking technologies, companies reduce costs, increase accountability, and build a foundation for innovation that scales across all departments and sites. As industrial sectors face mounting pressure to be more efficient, more sustainable, and more agile, embracing the latest in asset tracking will be crucial for staying competitive and secure in an increasingly digital world.
Source: The Future of Asset Tracking in Industrial Environments